Protecting Pressure Instruments in Suction and Discharge Installations
water & wastewater | flow restrictors | diaphragm seals | liquid filled gauge | instrument assembly | dampening device
If you work in a chemical manufacturing facility, water treatment center or oil/gas refinery, you likely use pump systems to transfer products between different stations. Suction and discharge installations can be particularly problematic environments for the instruments used to monitor the pressure in these systems. If your instruments get damaged, the entire process can break down, so protecting them is a priority.
Ashcroft has been a major contributor to water/wastewater pressure and temperature instrumentation for decades, so we understand the challenges of keeping instruments protected in harsh environments. Read this article for our recommendations for keeping your pressure gauges, switches, and sensors working properly, regardless of where they are positioned during pump system installations.
Once you have finished reading, you will be equipped to determine the most suitable approach for your needs. Additionally, you will have access to relevant articles and guides to help keep your systems running smoothly.
Common instrumentation challenges in pump system installations.
Pressure gauges, switches and sensors are commonly found on both the suction and discharge sides of pump systems. They may be directly connected to the process or isolated using diaphragm seals or isolation rings.
Pumps often cycle on and off. This is typically an automated process that can lead to pressure transients with the potential to damage your pressure gauges, switches and sensors.
Sudden surges of pressure, when pumps start, can exceed the proof pressure of instrumentation, while the shutdown momentum can cause a water hammer effect, resulting in pressure spikes that may damage unprotected devices. Although these pressure transients are harmful and can initially be hard to predict/detect, they are not the biggest problem associated with pump systems. Pump systems are notorious for creating both vibration and pulsation in instruments that are close to the pump.
Strategies for addressing instrument challenges in pump systems.
For Mechanical Pressure Gauges
There are several ways to protect mechanical pressure gauges in harsh conditions associated with pump systems. Following these strategies can help ensure pressure gauge effectiveness and extend the life of these instruments.
1. Install ASME B40.100 recommended protection devices directly to the process. Examples include:
- Pressure snubbers and pulsation dampeners protect gauges by absorbing sudden changes in pressure that commonly occur in pump systems. Using these devices can help ensure the accuracy and reliability of your pressure instruments and extend their life span.
- Pressure-limiting valves prevent pressure from exceeding a pre-determined set point and will only reopen once the pressure drops down below a certain value. This helps create a more stable and controlled operating environment.
- Capillaries can be used in severe cases when instruments need to be removed from direct contact with the installation point to protect them from vibration, pulsation and elevated process temperature.
2. Use a liquid-filled gauge case.
Gauge cases that are filled with glycerin, silicon, or halocarbon are also helpful in dampening the effects of pulsation and vibration in these applications. They also keep moisture out of the case and condensation off the window while lubricating the internal mechanical components of the gauge. However, keep in mind that liquid-filled gauges also have a risk of leaking due to high vibration or excessive change in temperature, especially if installed outside.
3. Use a dry gauge with an internal dampening mechanism.
An alternative to a liquid gauge is to use one of the Ashcroft® pressure gauges featuring PLUS!™ Performance. This gauge is engineered with an internal dampening media and offers the same effect as a liquid-filled gauge but without the risk of leaks.
4. Add throttle screws or plugs into the pressure connection.
Whether you have a dry gauge, liquid-filled gauge, or dry gauge with PLUS!™ Performance, we recommend throttle screws to help manage pressure pulsations. These devices (also referred to as plugs) are inserted in the orifice of the pressure connection to significantly reduce the orifice size and minimize the impact of pulsations.
5. Keep the pressure gauge span between 25% and 75% of full scale.
When selecting the span for your pressure gauge, ASME B40.100 guidelines recommend keeping the normal operating pressure between 25% and 75% of full scale. While this remains consistent across pump system applications, leaning toward the 25% mark can be beneficial. Opting for a larger range accommodates pressure transients and also helps minimize the effects of pulsation and vibration. A smaller pressure span can leave mechanical pressure gauges more susceptible to these challenging conditions.
For Mechanical Pressure Switches
With mechanical pressure switches, it is harder to notice the effects of pulsation and vibration. Although these are industrial products, they are still carefully calibrated instruments that can be impacted by these conditions. The effect of pulsation and vibration tends to cause switches to trip sooner than the calibrated set point. This is why using pulsation dampeners and pressure snubbers helps protect these instruments. In cases of extreme vibration, pressure switches can be remotely mounted using capillaries.
For Diaphragm Seal Assemblies
As mentioned previously, all instrument protection devices can be installed directly into the process or isolated using a diaphragm seal or isolation ring. These isolators serve to protect the instruments from various hazardous conditions such as clogging, corrosion, or extreme temperatures. While diaphragm seals do offer some dampening, it is often recommended to include additional dampeners or snubbers along with PLUS!™ Performance to protect the instruments effectively.
Assemblies can accommodate at least one, and sometimes several instruments. However, if there are multiple instruments, all instruments must have the same range, which is the widest range possible while still maintaining the normal operating range within 25-75% of the dial (for pressure gauges). A broader range provides better protection for the instruments, and when installed on a diaphragm seal, they exhibit better responsiveness to pressure fluctuations.
Note: Low-pressure systems may experience sluggishness when isolated with a diaphragm seal. Ultimately, the instrument's performance depends on the pressure exerted on the isolator's sensing element to displace enough fill fluid to operate the instruments, which can be challenging with lower pressures.
Figure 1. Ashcroft® Diaphragm Seal Assembly.
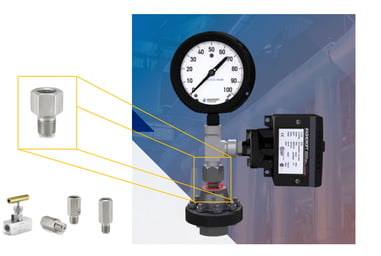
Digital pressure gauges and sensors (transducers and transmitters)
Digital pressure gauges and pressure sensors can be much more forgiving under challenging circumstances. These instruments are engineered to handle over-pressure conditions and the effects of vibration are not as detrimental as they are on mechanical products. Often sensor-based instruments can slow down the reaction time to minimize the effects of pressure pulsations.
Ready to learn more?
Now that you have a few strategies for protecting your pressure gauges, switches and switches from the harsh conditions found in pumping systems, you can determine which of these devices help address your specific challenges. For further insight, we recommend the following articles that may also be of interest to you.
- Liquid-filled vs. Direct Drive Pressure Gauges vs. PLUS!™ Performance
- Ashcroft PLUS!™ Performance Product Guide
- When to Use a Dampening Device with a Diaphragm Seal?
- Do Measurement Instrument Accessories Affect Accuracy?
Of course, you can also speak with a product expert to get answers to any questions you may have. In the meantime, download our guide to learn more about helpful instrument devices and assemblies.
About John Girard, Business Development Dealer
John Girard is currently the Business Marketing Leader for Diaphragm seals, Process Gauges and Accessories at Ashcroft. Formerly, he was the Territory Sales Manager responsible for supporting the distribution network in the Northeast. He began with Ashcroft as a Product Specialist for mechanical pressure gauges and accessories. He transitioned to a Sales Engineer role working with engineering firms on specifications. John achieved an M.B.A from Johnson & Wales University and has 10+ years of experience working with Sales and Marketing.