What to consider when choosing material for your diaphragm seal
This article was originally published on April 8, 2024, and updated on September 30, 2024.
Oil & gas, water/wastewater, chemical and petrochemical industries rely on accurate and repeatable pressure measurement instruments to ensure processes run safely and efficiently. However, without proper protection, the internal (wetted) components of those pressure gauges, transmitters, transducers and switches will become damaged from the corrosive materials found in these harsh applications.
Diaphragm seals are the ideal solution for protecting your pressure sensors from potential damage because they can isolate the sensing components from the process media. But choosing the right diaphragm seal for the job requires you to consider which wetted materials are best suited for your specific application. Ashcroft can help. We have been an industry leader in pressure and temperature instrumentation for decades and often help our customers address this very challenge.
In this article, you will learn the four factors to consider when choosing your diaphragm seal material. When you are done reading, you will have the information you need to be more confident in your purchasing decision. You will also see additional related resources to address other diaphragm seal questions you may have
.
Why diaphragm seal material matters.
Although there is a lot to the diaphragm seal manufacturing process, making them in different materials is relatively easy. On the other hand, making pressure instrument sensing elements is much more complex.
For example, an actuator assembly on a pressure switch, or a bourdon tube on a pressure gauge, rely on the size, dimension, elasticity and resistance to provide specific movements for accurate pressure readings. Finding the right combination using a variety of exotic materials such as tantalum or Hastelloy® would range from difficult to impossible. So, when those or other exotic materials are required, diaphragm seals are used to protect those instruments from harsh conditions.
Components of a diaphragm seal.
Though the exact components will vary, most diaphragm seals will share the same essential parts.
Figure 1. Diaphragm seal components.
Most designs include:
- a top housing that connects the instrument to the diaphragm.
- The fill port that lets the assemblies be vacuum filled with fluid.
- a lower housing that connects the diaphragm to the process piping.
- a diaphragm that transmits the process pressure to the instrument.
Lower housings have a wide variety of connection options, including flanged, threaded and welded. As you can see, the only two parts that touch the process are the diaphragm and the lower housing.
There are also options like the Ashcroft® DF Flush Flanged Diaphragm Seal that do not have a lower housing for a less costly alternative.
Figure 2. Diaphragm seal connection types.
Wetted parts compatibility and other primary drivers in material selection.
Whether or not a diaphragm seal has a lower housing, it is important to consider the wetted parts material and how they interact with the process. Wetted parts compatibility is the primary driver when selecting materials, however there are also other factors. Here are the top four considerations:
1. Compatible materials.
Diaphragm seal assemblies often involve several components for different functions. The primary component, being the instrument, would be installed either directly on the seal or on an accessory. Examples of accessories include a temperature dissipator, capillary for remote mounting, dampener or t-fitting to connect multiple instruments.
Whether the instrument pressure connection is installed directly on the seal or to an accessory, the materials must not lend themselves to corrosion. We recommend similar materials to limit the number of possible variables/reactions between our product and the media. Sometimes we have mixed materials to provide better corrosion resistance on thinner-walled products like diaphragms.
-
-
For threaded connections, we recommend materials that are close together on the galvanic series, which determines the electrochemical potential of metals/alloys. When they are too far apart it can create an accelerated corrosion of the more active metal, or an anode (galvanic corrosion). This effect primarily occurs with an electrolytic solution such as salt water but can be seen elsewhere. Threaded connections usually provide more places for the media to stay stagnant which increases the rate of corrosion.
-
With welded connections, which reduce the likelihood of leak paths, selecting chemically robust and compatible materials throughout the assembly is also critical. For example, welded Hydrofluoric Acid (AF) Alkylation Units, often referred to as HF Alky units, commonly use Monel® materials for their instruments, which are suited best for installation on Monel® accessories and Monel® top housings with Monel® diaphragms and lower housings.
The Ashcroft® Acid Leak Detection (ALD) gauges are designed for these types of situations. In the case of Monel®, every part that is welded must all be the same material. Other materials like 316L Stainless Steel, Hastelloy® and Tantalum can be mixed. However, when the installation is not welded, having two unlike metals in contact can create premature rusting, especially when installed in high-humidity areas.
-
2. Material temperature and pressure limits.
Diaphragms and lower housings can be made of both metallic and non-metallic materials. When it comes to temperature limitations, the metallic configurations are not usually a factor as the limitations would more likely be tied to the system fill fluid or other factors.
For the non-metallic materials, however, it is a different story. The non-metallic options that may be exposed to the process could include materials like PTFE, Viton™, Kalrez®, PVC, PVDF, CPVC, Acetal or EPDM. It is important to consider both the material temperature limit as well as the degradation of that limit as pressure increases.
Figure 3. Non-metallic diaphragm seal temperature limits.
Figure 4. Non-metallic lower housing material temperature limits.
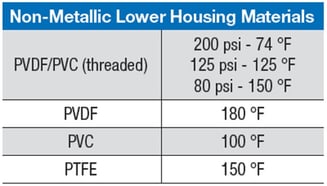
Although these materials are limited in terms of temperature, they may be an ideal option for situations with strong chemical resistance or flexibility. Flexibility is critical for low-pressure applications or applications that require low-pressure set points on switches.
3. Material availability.
If you’re specifying material requirements for your application, it is important to consider material availability. When there may be multiple options from a compatibility, pressure, and temperature perspective, you may want to choose the readily available options.
Some exotic materials, although necessary, can be difficult to source and can create limitations on diaphragm seal design, lower housing options (flush ports options) or available sizes. For example, PTFE materials cannot be used in smaller flanged assemblies whose designs have studs threaded into the lower housing. Also, for tantalum-clad lower housing, the plating process can be difficult, so allowing for a variety of materials in your specifications can help open up other options.
4. Material cost.
Although this is a factor, it must be prefaced with the understanding that this is the least important factor. Compatibility and structural integrity - as they relate to pressure and temperature limitations - and compatible materials are the most critical considerations. Availability is a distance third, and cost is way down at the bottom of the list. However, cost can still be a factor when you have several options that will suffice.
For example, low-pressure ranges require a flexible material on standard diaphragm seal designs (versus high displacement designs). At Ashcroft, we offer Viton™ and Kalrez® for flexible diaphragm materials. Kalrez® is significantly more expensive and should only be used when required for compatibility purposes.
5. NSF/ANSI/CAN 61-certification requirements (when needed).
When choosing diaphragm seals, or any instruments used in potable water systems, public health is a primary concern. That's why potable water systems must only use components that meet the requirements of NSF/ANSI/CAN 61 to ensure the water is safe for public consumption.
Ashcroft offers NSF 61-approved diaphragm seals and other instruments for use in potable water applications. These certifications verify that our products meet the stringent health effects requirements for drinking water system components and underscore Ashcroft’s commitment to product safety, quality, and public health.
Want to know more about diaphragm seal selection?
Now that you know what to consider when choosing wetted material for your diaphragm seal, and why material selection is important to help protect your pressure instruments from harsh applications, you may have more questions. We’ve compiled a few extra resources that may be of interest to you:
- Diaphragm seal min/max guide
- How do I safely select diaphragm seals for high-temperature applications?
- When to use a diaphragm seal vs. and isolation ring
- What factors affect a diaphragm seal's performance?
- Understanding NSF/ANSI/CAN 61 Approvals for Pressure Instruments
And of course, feel free to contact us with any questions or concerns you may have. In the meantime, download our guide to learn more about selecting an instrument assembly solution for your specific needs.
About Darren Lewandowski, Territory Sales Manager
Darren Lewandowski is the Territory Sales Manager (Channel/Distribution) at Ashcroft, responsible for the Northeast U.S., from Maine to Maryland. He started his career at Ashcroft in 2018 with 16 years of experience with flow control and measurement. He currently works with distributors and their end users in many areas, these include water/wastewater, food and beverage, high purity, and pharmaceutical to name a few, with a focus on providing solutions. In his leisure time, Darren enjoys traveling with his wife of 27 years, and proudly watching his daughters grow up to be wonderful and accomplished young women.