Protecting Monel Pressure Gauges from Stress Corrosion Cracking in Hydrofluoric Applications
Hydrofluoric acid (HF) is well known for its aggressive and hazardous characteristics. That’s why selecting material for these applications is important for ensuring the safety and performance of your instruments and your operation.
Ashcroft is a recognized leader in pressure measurement instrumentation and understands the unique challenges of hydrofluoric acid (HF). Read this article to learn about stress corrosion cracking, the comparative properties of Monel® 400 and Monel® K-500, their performance in HF environments, and considerations for using these or alternative materials in applications where corrosion resistance is critical.
What is stress corrosion cracking?
Stress corrosion cracking (SCC) happens when materials are under mechanical stress, such as tension or compression, in a corrosive setting. This type of cracking can be exacerbated by residual stress from forming, welding, or external loads applied to an alloy. Identifying SCC in a process is challenging because the cracks are microscopic, often only becoming apparent after a catastrophic failure has occurred.
Figure 1. Example of stress corrosion cracking.
How do Monel 400® and K-Monel® 500 compare in HF applications?
Hydrofluoric acid poses a unique challenge because it is both highly corrosive and prone to triggering stress corrosion cracking, especially when oxygen is present in the vapor phase. Research has demonstrated that while both Monel 400 and Monel K-500 are susceptible to SCC in HF, the differences are subtle and application-specific:
- Monel 400, a predominantly nickel and copper alloy, is commonly used in environments where corrosion resistance is essential. Studies suggest that Monel 400 exhibits slightly better SCC resistance in HF vapors compared to Monel K-500, particularly in aerated acid. However, this advantage is minimal.
- Monel K-500, a precipitation-hardened version of Monel 400, is distinguished by its increased hardness and tensile strength. However, this higher strength can also make it more susceptible to SCC, particularly in age-hardened conditions. According to the Nickel Development Institute, Monel K-500 may experience SCC more rapidly in moist HF vapors, especially when cupric fluoride deposits are present. Nevertheless, Ashcroft's pressure gauges use K-Monel Bourdon tubes which are stress-relieved rather than age-hardened, which partially mitigates this risk.
Avoiding SCC in HF applications: key considerations and recommendations
For HF service, both alloys are highly vulnerable in the vapor phase when oxygen is present. Because HF alkylation units are designed to exclude oxygen, this reduces the corrosion risk to some extent. However, even a trace amount of trapped oxygen can catalyze SCC, especially in high-stress areas like the Bourdon tube of pressure gauges.
Diaphragm seals help isolate pressure gauges from direct exposure to HF vapors, offering an additional layer of protection. For HF applications, it is recommended to use a combination of a Kynar® or Monel lower housing, a Halar®-coated Monel diaphragm, and a Monel gauge for secondary containment.
Additionally, our Acid Leak Detection (ALD) assembly products can provide visual indications of leaks, offering an extra layer of safety in critical applications.
Recommendations for HF service applications
1. Use oxygen-free environments
Exclude oxygen in HF service environments as much as possible to prevent SCC. If oxygen-free conditions cannot be ensured, a diaphragm seal should be installed.
2. Order gauges to Ashcroft variation
For direct HF service, selecting Monel wetted components with Ashcroft® variations X6A is recommended, as they ensure gauges are free from residual water. Additionally, liquid-filled or throttled gauges, such as Ashcroft® PLUS!™ Performance gauges, are essential to dampen vibrations and pulsations that could accelerate SCC. Choose gauges with a full-scale pressure rating of approximately twice the intended operating pressure. Limit maximum pressure to 75% of the scale range to minimize stress on the elastic element (e.g., Bourdon tube or bellows).
3. Evacuate and backfill the Bourdon tube
When installing a new gauge, it’s crucial to evacuate and backfill the Bourdon tube with an inert gas or liquid, eliminating any residual air. Even a small amount of oxygen in the tube can increase SCC risk, as it becomes trapped in the most highly stressed area.
4. Use diaphragm seals for extra protection
For added protection against SCC, diaphragm seals made of corrosion-resistant materials, including options like Halar® (ECTFE) or even gold plating, can be used to further isolate gauges from HF exposure. A common recommendation for HF applications includes a combination of a Kynar or Monel lower housing, a Halar-coated Monel diaphragm, and a Monel gauge for secondary containment.
5. Incorporate acid leak detection
ALD gauges like the ones offered by Ashcroft, are designed with a special yellow coating that changes to red once it is exposed to acids with a pH of ≤ 3.
By following these recommendations and leveraging the right materials, industries can ensure safer operations and longer equipment life in the demanding environment of HF alkylation units.
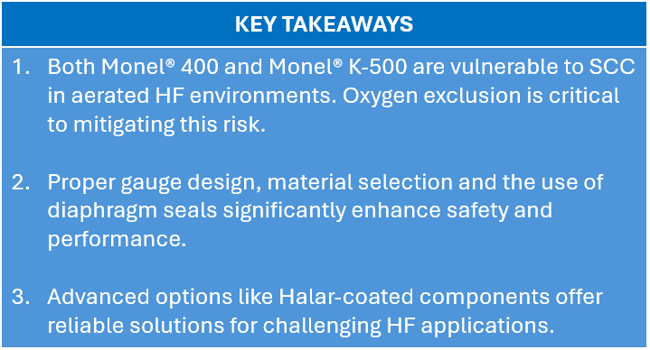
Ready to learn more?
While both Monel 400 and Monel K-500 are viable options for HF service, controlling environmental factors and adhering to best practices in installation and maintenance are key to maximizing their lifespan and performance. For those needing extra security, alternatives like diaphragm seals or even specialty coatings may provide the added layer of protection necessary to safely handle hydrofluoric acid applications in refinery settings.
For your reference, here are a few more articles that may be of interest to you:
- Acid Leak Detection (ALD) video
- Safe Instrumentation for the Chemical Industry
- Best Pressure Gauges for Ammonia Plant Applications
- How to Protect Instruments from Different Types of Corrosion
If you have any questions, feel free to contact our product experts who can provide the answers you need for your application. In the meantime, download our solutions guide for the chemical and petrochemical industry.
About Alex Froning, Materials Engineering Manager.
Alex is the Materials Engineering Manager at Ashcroft. In this role, Alex is responsible for supporting product compatibility and manufacturing processes for the company's pressure and temperature instruments. His expertise is in materials science and engineering with a concentration in metallurgy.