Ways to Measure Pressure in Industrial and OEM Applications
If you are working in an industry that requires instrumentation to measure and monitor pressure in a system, you already know the basic principle of pressure measurement. According to Pascal's Law, pressure is proportional to the force and inversely related to the area over which the force is applied. In other words, pressure is equal to force per unit area.
Figure 1: Pressure Equation.
Different systems and applications require different types of pressure measurement instruments. For example, mechanical pressure gauges may be used as visual indicators of pressure levels throughout a process. Conversely, pressure transducers or transmitters can sense changes in a system’s pressure and send a signal to a control room. If you are new to your industry and want to learn more about pressure instruments, this article will give you a high-level overview of how to read pressure, definitions of pressure types and the instruments used to measure pressure.
Ashcroft is a recognized global leader in pressure instrumentation and is a trusted authority for related information. When you are done reading, you will find additional resources related to pressure measurement that may interest you.
How do you measure pressure?
In the U.S., pressure is measured as pound force per square inch or psi. Note, in other parts of the world, pressure is measured in different systems of units. The three main systems are the American System, Systeme International (SI) and the Meter, Kilo, Second (MKS). See below for a full list:
Figure 2: Pressure System of Units.
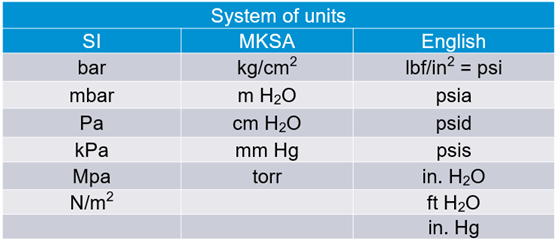
High pressure measurements generally range above 15 psi while low-pressure measurements range below 15 psi.
Figure 3. PSI Ranges.
Low pressure is best explained using a manometer as an example. In Figure 4 below, without any pressure applied to the open tube manometer, the water level is even on both sides of the tube. When you add a small amount of pressure from the bicycle pump to one side of the tube, it displaces the water in the tube.
The side with the pressure applied goes down while the other side goes up. When you measure the total displacement, you measure the pressure applied. In this example, the displacement is 4 inches, so the pressure applied is 4 inches of water.
Figure 4: Low-Pressure Manometer.
Types of pressure measurement.
Absolute Pressure. A measured reference to absolute vacuum (zero pressure). Absolute vacuum occurs when air is completely absent. There is no negative absolute pressure.
Figure 5: Absolute Pressure.
Gauge Pressure. A positive pressure greater than atmospheric or barometric pressure using ambient pressure as the reference.
Vacuum Pressure. A negative pressure less than atmospheric or barometric pressure using ambient pressure as the reference.
Figure 6: Gauge and Vacuum Pressure.
Note: there may be specific requirements for gauges that measure both positive pressure and negative pressure, also known as a gauge with a compound range or scale.
Differential Pressure. The difference between two different pressure points in a system. This is often called “DP”, “∆P” or “DeltaP”.
Figure 7: Differential Pressure.
Static Pressure. The maximum working pressure (MWP) in a system with or without flow.
Single-Sided Static Pressure. The maximum pressure that can be applied to one side of an instrument while the other side is open to the atmosphere.
Proof Pressure. The maximum pressure a gauge can withstand without plastic deformation of the pressure element. (ASME B40.100-2013)
Burst Pressure. The maximum pressure above which the pressure element assembly will no longer hold pressure.
Pressure measurement applications.
Depending on the application, your instrument will have different requirements for pressure type, psi and other factors. Here are just a few of the thousands of applications where you would expect to see pressure measurement instruments in your daily life.
Figure 8: Pressure Measurement Applications.
Whether your application is measuring high-pressure or low-pressure, Ashcroft offers an extensive range of measurement instruments to address your specific needs. For instance, our process gauges and industrial gauges provide visual indicators to operators, while our transducers with advanced sensing technology will communicate pressure measurements to a control system. Visit Ashcroft.com/products to our complete line.
Go beyond the basics.
Now that you know the fundamentals of pressure measurement are you ready to expand your knowledge? Here are a few related articles that can get you started.
• How Much Do Mechanical Pressure Gauges Cost?
• What is a Differential Pressure Gauge?
• Choosing a Pressure Gauge for Hydrogen Applications
• The difference between a pressure transducer and a pressure transmitter
If you prefer to speak with someone directly, feel free to contact one of our product experts with any questions you may have.
In the meantime, download our guide, 5 Mistakes to Avoid When Choosing a Pressure Gauge.
About Dave Dlugos, Product Technical Leader
Dave Dlugos has a BSEE degree and 40 years of experience in the measurement industry performing design engineering and product management. He has earned 4 U.S. patents and joined Ashcroft in 2007, currently as the Product Technical Leader. He is a senior member of the International Society of Automation (ISA), past ISA District 1, Vice President, past ISA water and wastewater division board member and the past President of CT Valley ISA Section.