What is a Diaphragm Seal?
If you are new to the world of diaphragm seals or just want a refresher on how they work, you've come to the right place. A diaphragm seal (also known as an instrument isolator) is a protective mechanism that connects to the process side of a pressure measurement instrument. The primary function of a diaphragm seal is to prevent the sensing element of your pressure instrument from getting damaged by any corrosive process media or clogging in your application. Without using a diaphragm seal in place to protect your instrument, you will not be able to accurately and effectively measure the pressure in your system, putting your entire operation at risk.
Why trust Ashcroft? We are an industry leader in pressure and temperature measurement instrumentation and are often asked for insight regarding the benefits of these instruments and how they work. In this article, I will review how diaphragm seals are used in different applications and provide links to additional resources in case you want to expand your knowledge on the subject further.
What industries use diaphragm seals?
You will find diaphragm seals in any industry where there is a risk of harsh chemicals, solids or other abrasive substances coming into contact with the pressure-sensing element of the instrument. Diaphragm seals can also be used to protect instruments from extreme temperature applications. However, high-heat applications pose unique challenges and temperature limits for these devices. If this is the case, a temperature dissipation device is generally used along with the diaphragm seal for best results.
Figure 1: Industries that use diaphragm seals.
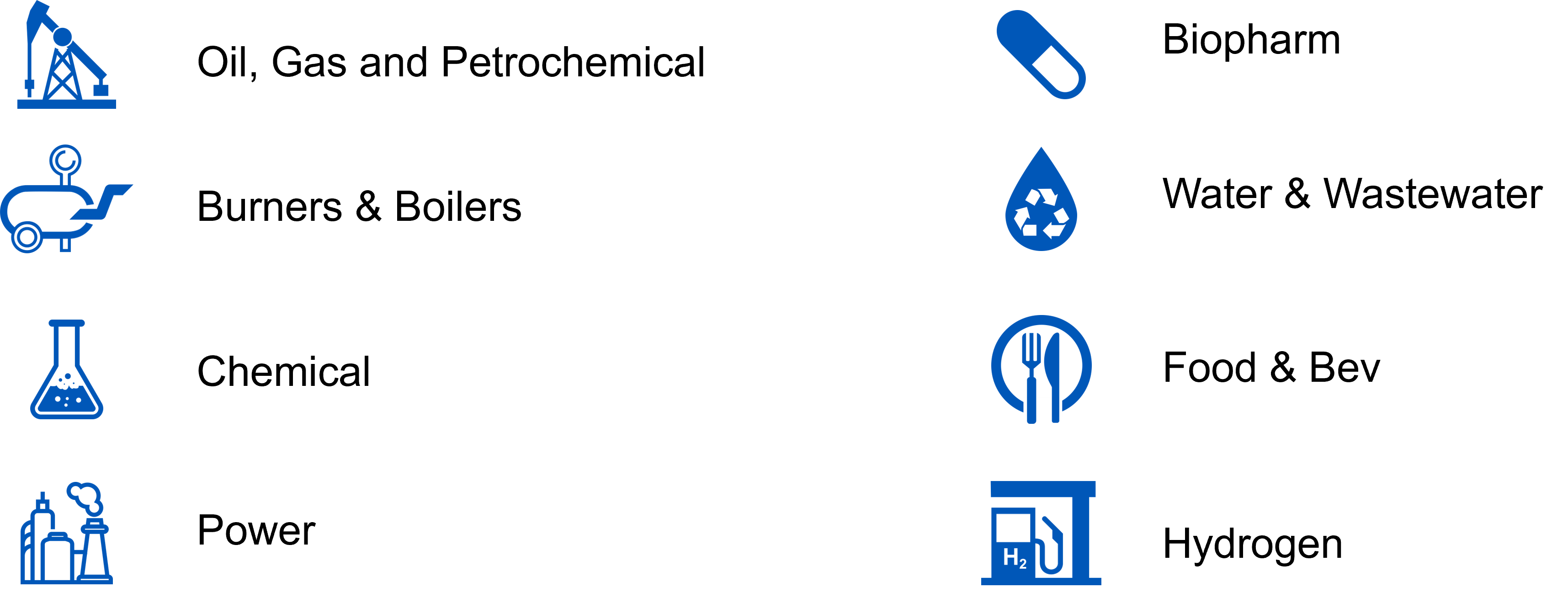
How does a diaphragm seal work?
As we mentioned above, the diaphragm seal connects to the process side of pressure measurement instrument. The seal's job is to isolate the measuring instrument from the process fluid while still conveying pressure changes through a flexible membrane.
Here's how:
- The space created by the diaphragm, upper housing, and the measurement device is filled with a fluid that transfers pressure.
- When there's a pressure variation at the process connection, the diaphragm flexes, causing the transfer fluid to move.
- This movement then conveys the pressure change to the instrument's pressure-sensing element.
The exact components of a diaphragm seal will vary between specific models. However, most of these devices share the same basic parts:
The function of each diaphragm seal is as follows:
-
The top housing serves as the connection point to the pressure measuring device.
-
The fill port lets the assemblies be vacuum filled. Then a ball bearing is placed into a conical seat to seal it, using a set screw to secure it.
-
The diaphragm isolates the process fluid from the filling fluid, making it the component that comes into direct contact with the process. It can be either welded or screwed into the upper housing, which itself may be welded or clamped onto a lower housing. Pressure variations lead to the diaphragm's deflection. This in turn displaces the fill fluid and conveys the pressure changes to the pressure-measuring device.
-
The lower housing connects a diaphragm seal to the process. This part of the diaphragm seal is available in different thread sizes or can include threaded flushing connections. These can be used to clean the inside of the seal or flush out any process media.
-
The fill fluid is also known as system fill or pressure sensing fluid. The fill fluid is necessary to transmit pressure changes from the diaphragm membrane to the pressure sensing device.
-
A flushing port is sometimes needed to clean process media that may be clogging the seal.
-
Diaphragm seal assemblies are filled using a vacuum filling process. This is done to ensure the system is void of air gaps. The fill fluid you use is determined by the operating temperature and other conditions of the application.
-
The lower clamping ring holds the assembly together.
Note: the diaphragm material, lower housing material and the fill fluid must be all be compatible with the process media.
Considerations for diaphragm seal material selection.
There are two primary considerations for deciding which material to select. The first is to choose the material that is most compatible with the process media of your application. Diaphragm seals are offered in multiple configurations with a wide selection of wetted materials that are compatible with most process media. The most compatible for corrosive process media include 316 stainless steel, Monel® and tantalum. Be sure to consult the manufacturer's compatibility recommendations or speak to a product expert.
The second consideration is to select the material that will work within the operating pressure and temperature limitations of your operation. Note: low-pressure applications (if the pressure range is less than 30 psi) will require either a very flexible diaphragm material or a large surface area to handle mechanical products with low-pressure range or high displacement instruments.
For more information on the minimum spans and maximum allowable working pressure (MAWP) of certain pressure instrument configurations, you can refer to the Ashcroft Diaphragm Seal Pressure and Temperature Min/Max Guide.
Ready to go beyond the basics?
Now that you know what a diaphragm is and how it works to protect your pressure instruments in harsh applications, you may be ready to learn more. Here are a few more related articles that you may find helpful.
- What factors affect a diaphragm seal's performance?
- How do I safely select diaphragm seals for high-temperature applications?
- When to use a diaphragm seal vs. and isolation ring
- Why use a flushing connection on a diaphragm seal?
Feel free to contact us with any questions or concerns. In the meantime, download our guide to learn more about selecting an instrument assembly solution for your specific needs.
About Dave Dlugos, Product Technical Leader
Dave Dlugos has a BSEE degree and 40 years of experience in the measurement industry performing design engineering and product management. He has earned 4 U.S. patents and joined Ashcroft in 2007, currently as the Product Technical Leader. He is a senior member of the International Society of Automation (ISA), past ISA District 1, Vice President, past ISA water and wastewater division board member and the past President of CT Valley ISA Section.