What is a Thermowell?
A thermowell is a device designed to protect temperature monitoring instruments from the damaging effects of corrosive media, high pressure and velocity in industrial applications. Without the protection of a thermowell, temperature instruments can become inoperable, putting your whole operation at risk.
Ashcroft is a global leader in temperature measurement instrumentation. We created this article as part of our Understanding the Basics series to provide a foundation of information about thermowells. If you are an industry novice or just want a refresher on how thermowells work, this is a great place to start.
In this article, you will discover where thermowells are used, learn about the different types of thermowells, see how they connect to the process piping and more. When you are done reading, you will also find additional resources that may interest you.
How are thermowells used?
Thermowells are made from solid metal bar stock with an opening on one where you insert the temperature instrument, such as a bi-metal thermometer, gas-actuated thermometer, RTD or thermocouple. The thermowell acts as a heavy metal jacket that prevents corrosion, system pressure and high-velocity flow from damaging the instrument’s probes, stems or bulbs. By protecting these instruments against the dangers of your application, thermowells are also protecting your process equipment and your people.
You can find thermowells in industrial applications that require monitoring extreme temperatures of air, gas or liquid in challenging environments. Examples include:
Figure 1. Extreme temperature environments.
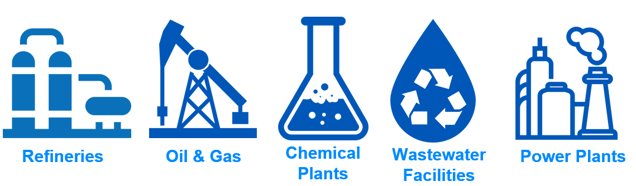
What are the primary elements of a thermowell?
Here are the functional parts of a thermowell, starting from the top of the instrument.
Figure 2. Different Parts of a Thermowell.
How to select the appropriate thermowell for your application?
When selecting a thermowell, there are many factors you need to consider:
Material compatibility
Thermowells are made with many types of materials and grade levels. Materials range from standard steel, Stainless steel, duplex stainless, and exotic materials like Monel, Inconel, chrome molly and others. Before you choose which is the best for your applications, you must:
- Verify your material selection is compatible with your process media, as well as the application’s piping or vessel.
- Consider the process media temperature. The process media temperature can play an important role in corrosion.
- Know the effects of process flow on the thermowell. Thermowells typically fail from vibratory stress, caused by the process flow, not the effects of temperature and pressure as so many believe.
Connection types
After you have selected the thermowell material that is compatible with your process media, you will need to determine how you want the thermowell to connect to the process. There are many connection types to choose from, but we will focus on the three most common.
- Threaded. Threaded thermowells are typically threaded into your process.
Figure 3. Threaded thermowell.
- Flanged. Flanged wells bolt to a flange that is usually installed onto a nozzle or tee attached to your piping or vessel. Flanges come in various sizes, face types and pressure ratings most commonly per ASME B16.5.
Standard sizes are 1, 1 ½ or 2 inches, face types are raised face, flat face or ring joint with pressure ratings of 150#, 300#, 600# and higher ratings. If required -- EN flanges for the European markets and custom flanges are also available to meet the various demands in the marketplace.
Figure 4. Flanged thermowell.
- Welded. Welded thermowells are either welded directly into your vessel or pipe or welded into a sockolet that has been welded in place.
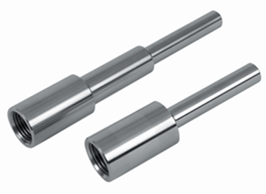
Shank types
This is the portion of the thermowell that is inserted into your process. Shank types are either straight, stepped and tapered.
-
Straight shanks are the original shank design for a protection tube or thermowell. This has the same outer diameter (OD) from the root to the tip. They are the strongest well.
- Stepped shanks have a smaller diameter wall at the tip than at the root of the well, providing stiffness along with a quicker response time as the 1st 2 ½ inches have a reduced OD to improve heat transfer.
- Tapered shanks have a smaller tip diameter than the base or root of the thermowell and are typically the most common due to their superior strength, vibration resistance and response time.
Figure 6. Different types of shanks.
Understanding the effects of flow.
As mentioned previously, thermowells typically fail from vibratory stress, not the effects of temperature and pressure. The figure below gives you an idea of the turbulence that can be created by flow in your application.
To determine if your thermowell is properly suited for your application, a standard has been developed to calculate the effect of flow on the thermowell. This standard evaluates the forces caused by external pressure and the combination of static and dynamic forces resulting from fluid impingement. This is referred to as a Wake Frequency Calculation. The standard it follows is ASME PTC 19.3 TW.
Figure 7. Wake Turbulence.
A wake is the region of recirculating flow immediately behind a moving or stationary solid body, caused by the flow of the surrounding fluid. The alternating vortices that occur as the media flows across the shank create turbulence. This causes the thermowell to resonate or oscillate. This is referred to as vortex shedding or Von Karmen trail.
The shedding rate is calculated and compared to the natural frequency of the thermowell. If the frequency of the wake is too close to the natural frequency of the thermowell the vortex shedding can destroy the thermowell, resulting in possible damage to the temperature instrument and further down your process as the broken shank flows through your system.
Ashcroft has a Wake Frequency Calculator to help you design your thermowell to meet your application.
Go Beyond the Basics.
Now that you have a basic understanding of thermowells and how these sensors work with temperature instruments in different applications, you may be ready to dig in a little deeper. Here are a few related articles that can get you started.
- Fitting a Thermowell to Bimetal Thermometers, RTDs or Thermocouples
- How Much Do Thermowells Cost? 5 Factors that Influence Price
- What is a thermowell Wake Frequency Calculator?
In the meantime, feel free to contact us today to talk to one of our industry experts with questions or download our webinar to learn more.
About Dave Dlugos, Product Technical Leader
Dave Dlugos has a BSEE degree and 40 years of experience in the measurement industry performing design engineering and product management. He has earned 4 U.S. patents and joined Ashcroft in 2007, currently as the Product Technical Leader. He is a senior member of the International Society of Automation (ISA), past ISA District 1, Vice President, past ISA water and wastewater division board member and the past President of CT Valley ISA Section.