When to Use a Welded Instrument Assembly
pressure gauge | measurement instrument accessories | diaphragm seals | instrument assembly
This article was originally published on April 18, 2022, and was updated on April 17, 2024.
No matter what industry you work in, diaphragm seals (also referred to as isolators) and welded assemblies are used to protect your pressure and temperature instrumentation from corrosive process media.
After decades of making quality pressure and temperature gauges and sensors to help keep processes performing reliably and efficiently, Ashcroft has seen just about every scenario where something can go wrong. One reason we like to share our expertise is to help people like you who may be experiencing a similar issue that we can help solve.
In this article, you will learn what a welded diaphragm seal assembly is and how it is used to help mitigate the damaging effects of high temperature, pulsation and vibration endured by your instruments. You will also see how these assemblies can ensure reliable and accurate pressure readings of your process.
When you are done, you will find links to additional resources that can help you learn more about related topics.
What is a Welded Instrument Assembly?
Simply put, a welded instrument assembly consists of a mechanical measurement instrument like a pressure gauge and an accessory welded together to provide the specific protection you need. Different conditions and product specifications call for different accessory assemblies. For example:
For corrosion and clogging protection.
- A diaphragm seal/isolator. Protects the gauge sensor from corrosive process media and prevents clogging of the instrument from a dirty process.
Figure 1. Ashcroft®
For pulsation protection.
-
A pulsation dampener. Protects measuring instruments from sudden increases and fluctuations of pressure.
Figure 2. Ashcroft® Pulsation Dampener.
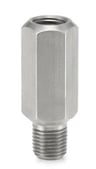
For elevated temperature protection.
- A finned siphon. The reduced orifice decreases the volume of the process medium in the siphon allowing efficient heat transfer between the medium and the siphon.
Figure 3. Ashcroft® Finned Siphon.
- MicroTube™and Mini MicroTube Siphon. The reduced internal volume of these accessories allows for superior temperature dissipation.
Figure 4. Ashcroft® MicroTube™ and Mini MicroTube™ Siphon.
- A capillary line. This accessory prevents direct contact between the gauge and the installation point to protect it from elevated temperatures or pressure spikes.
Instruments attached directly to seals can be welded, and assemblies with some accessories can be welded at each connection. However, there are some exceptions. Accessories like snubbers that help protect gauges from pulsation issues, and valves that help with isolation valves cannot be welded since they contain elastomers that will be compromised with the elevated weld temperature.
Figure 6. A Welded Instrument Assembly Example.
Why material compatibility is important in welded assemblies.
Materials that will be welded together must be compatible. For example, 316 Stainless steel cannot be welded to Monel. If the materials are not compatible, the instrument can be compromised and become ineffective. The good news is there are many material options available for the wetted portion of a diaphragm seal to ensure compatibility with the process media
How instrument accuracy is affected
Generally, an accessory attached to a gauge does not change the accuracy of the gauge. However, attaching a diaphragm seal/isolator to a gauge can typically reduce the gauge accuracy by ± 0.5% of span.
When it is necessary to weld a gauge to a diaphragm, Ashcroft confirms appropriate assembly accuracy tolerance after the assembly is welded, filled and calibrated. For example, an Ashcroft® 1279 Pressure Gauge with an accuracy of
± 0.5% when it is attached to a diaphragm seal, will usually have an accuracy of ±1% of span.
If the same Pressure Gauge is welded to a MicroTube™ Siphon and a Threaded Diaphragm Seal and then filled and calibrated, the typical gauge accuracy of the assembly will also be ± 1% of span. So, additional accuracy occurs only when a diaphragm seal is added to the assembly.
Why Use a Welded Instrument Assembly?
More and more customers are seeing the value of a welded instrument assembly. A welded instrument assembly can be used in any application and is good for all industries.
Prevents accidental tampering or disassembly. A welded assembly is tamperproof and prevents a diaphragm seal from being detached from the gauge. This is important because removing the gauge from the seal breaches the assembly's system integrity and will render the gauge inoperable.
The tamperproof welded design also prevents an important accessory from being removed. For example, if the process temperature is 800 °F/427 °C, design engineers may specify that a siphon needs to be attached to the assembly to dissipate process temperature and protect the gauge. If the siphon is removed from an assembly that is not welded, the gauge will lose its integrity and not give an accurate process pressure reading.
Primary benefits to welded assemblies.
A welded assembly provides peace of mind that the components of the assembly won’t be removed. Here are a few other reasons why a welded assembly can benefit you.
Note: If at some point welded components need to be replaced, replacement of the complete assembly would be required. Replacing individual instruments and accessories of a welded assembly is not an option. Breaking any welded connection of an assembly would result in damage to the instruments and accessories.
Ready to learn more?
Now that you understand the benefits and uses of welded instrument assemblies, you are in a better position to select the right solutions for your process to protect your pressure-measuring equipment. The following are links to additional resources that may also be of interest to you:
- Pressure instrument mounting assemblies (webinar)
- What’s the Right Pressure Instrument Mounting Assembly for Me?
- Isolation Ring Assemblies for the Water/Wastewater Industry that are Accurate and Reliable
- Best Practices for Installing Flanged Diaphragm Seals
Of course, you can also contact us directly with any questions or concerns. In the meantime, download our Complete Guide to Pressure Instrument Assembly to view all the different assembly options available
About Bob Pierce, Territory Sales Manager
Bob Pierce is the Territory Sales Manager (Channels/Distribution), responsible for 6 states in the Southeast Gulf Coast region. He started his career at Ashcroft in 2018 with 25+ years of experience in the fields of Instrumentation and Control Valves. Bob has a Bachelor of Science degree in the School of Business from the University of Alabama – Birmingham.