Calibrating Low-Pressure Sensors in Critical Environments
Working in cleanrooms, operating rooms and critical environments found in pharmaceutical and other industries requires you to maintain a positive pressure to prevent contaminants from entering these spaces. The pressure level necessary to keep these areas contaminant-free is typically between 0.01 to 0.15 inches of water differential. There are also negative pressure applications such as isolation rooms that require you to maintain pressures to similar levels. So, how exactly can you maintain such precise conditions to ensure these environments are safe for use?
The solution lies in carefully choosing instruments specifically designed and calibrated for these critical environments, coupled with an understanding of the future calibration requirements necessary to guarantee precise and reliable readings over time.
During the past eight years as a product manager overseeing the low-pressure sensor product line at Ashcroft, I’ve helped customers address this very issue with great success. In this article, you will learn about critical environments, reasons why instrument calibration is needed and how Ashcroft makes the process easier than traditional methods. You will also be directed to additional resources that can help answer other common questions about this topic.
What defines a critical environment?
An environment is considered critical due to its sensitivity to contaminants and the necessity for precise conditions to maintain its purity. Whether we are talking about isolation rooms, laboratories, operating rooms or clean rooms, factors such as air quality, temperature, and pressure must be tightly controlled to ensure the safety and effectiveness of the space.
Figure 1. Critical environment examples.
Before being used, cleanrooms and other critical environments must meet the strict requirements set by international standards. As previously mentioned, depending upon the function of the critical environment, specifications can vary from a DP (differential pressure) of 0.01 to 0.15 inches of water. If the pressure is too low, there may not be enough air movement to contain particles. If the pressure is too high the air will move into places it shouldn’t be like ceiling joints, and it can become difficult to open doors.
Any deviation from these optimal conditions can lead to compromised results, potential hazards, or even catastrophic consequences. This is why maintaining highly accurate differential pressure measurements to monitor airflow is vital for these applications.
Pressure sensors with terminal point accuracy methods are pre-calibrated.
When selecting a pressure transducer for critical environments, accuracy is paramount. Without the ability to achieve and maintain a specified level of accuracy at all times, these environments can be compromised.
Look for sensors designed with the Terminal Point methodology. This is a precise and reliable approach used to calibrate pressure sensors at specific points, such as zero and span settings, to ensure maximum accuracy and consistency in pressure readings.
By incorporating terminal point methodology in pressure sensor design, transducers like the Ashcroft® DXLdp and GXLdp come with a ±0.25% span accuracy straight out of the box, inclusive of zero and span setting errors. This means that upon installation, these units are ready to go without the need for any initial calibration adjustments.
Note: Statistically derived accuracy methods like the "best fit straight line" (BFSL) approach do not include zero and span setting errors in their specifications. For example, a ±0.25% BFSL accuracy transducer could have potential errors of up to ±1.00% for each parameter (zero and span), necessitating the need for initial calibration by the installer to ensure accurate readings. By neglecting to account for these inherent inaccuracies, the precision and reliability of the pressure sensors may be compromised, ultimately impacting the overall effectiveness and safety of your critical environment.
When additional calibration may be needed.
Critical room instruments have regularly scheduled validations to ensure that everything is operating at optimal levels. This process can be costly and time-consuming and will determine if recalibration of the sensor is necessary.
For verification purposes, technicians need to disconnect the electrical cables and pressure sensor connections, adding to the complexity and time involved in ensuring the system's accuracy. If recalibration is required, the system will be shut down while the instrument is brought to another location for calibration before being reinstalled.
In-place calibration can save you time and money.
To make it easier for plant operators to check an instrument's accuracy and make adjustments without altering the entire system, Ashcroft offers an 'in-place" calibration solution. The Ashcroft® SpoolCal™ Actuator is an option available on the DXLdp and GXLdp. This "actuator valve" connects to a master testing device that confirms the current process pressure and performs calibration modifications if needed, without disturbing the process connections.
Figure 2. Ashcroft® DXLdp with SpoolCal™ Actuator.
Figure 3. Ashcroft® GXLdp with SpoolCal™ Actuator.
How the SpoolCal™ Actuator works.
The SpoolCal™ Actuator has three modes: Monitor, Calibrate and Off. In Monitor mode, the unit is turned 90 degrees counterclockwise to quickly verify pressure. In Calibration mode, the unit is turned 90 degrees clockwise to isolate from process pressure and allow for calibration adjustment.
The SpoolCal™ is not a standard feature but it can be specified for the DXLdp and GXLdp products if saving time and calibration cost is important.
Figure 4. SpoolCal™ Actuator functionality.
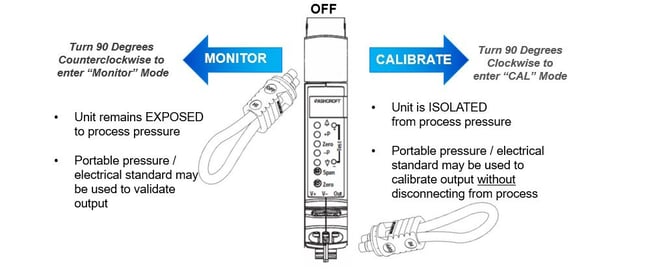
Want to learn more?
Now that you know why maintaining the precise pressure requirements of critical environments is essential, you can appreciate the importance of selecting the right instruments for the job. If you are interested in deepening your knowledge even further, take a moment to read these related articles.
- Choosing a Pressure Transducer for Critical Environments
- How Does Media Temperature Affect Pressure Transducer Performance?
- How Much Do Pressure Transducers Cost? (6 Factors Impacting Price)
You can also talk to one of our industry experts who can answer any questions that you have. In the meantime, download our guide to read about pressure instruments for critical environments.
About Mike Billingslea, Product Manager Low Pressure Transducers
Mike has 10 years of experience, specifically with Ashcroft low-pressure transducers, and has over 25 years of experience at Ashcroft in various Sales and Marketing roles. In his free time, he enjoys playing basketball and seeing live music.