How Much Do Pressure Transducers Cost? (6 Factors Impacting Price)
This article was originally published on May 10, 2021, and updated on April 2, 2025.
The industrial and OEM markets offer a wide variety of pressure transducers, each with its own price range. The challenge is finding the best instrument for your specific application at a cost that aligns with your budget.
Having spent over 20 years in the pressure sensor/transducer industry in roles related to product management and sales, I've gained firsthand knowledge of the numerous factors that affect pricing. In this article, you will gain insight into these cost drivers so you can make a more informed decision about your transducer purchase.
Please note, we are purposely excluding automotive/appliance and process transducers/transmitters from this discussion, as their market and cost structures are unique. Also, for clarity, the term “pressure transducer” refers to the complete assembly of the pressure sensor and output board, which some industries might also call a pressure sensor or transmitter. In this article, "pressure sensor" will indicate the sensing element or technology itself, which is part of the full pressure transducer product.
Pressure transducer cost ranges by market
Before we narrow down the cost factors by specific elements and options, here's a high-level view of transducer price ranges for a few select markets:
Figure 1: Pressure transducer cost ranges
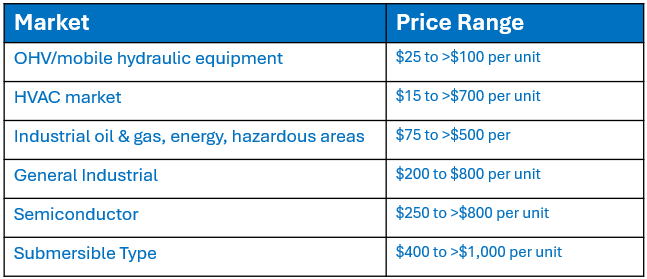
What are the primary pressure transducer cost drivers?
When considering the cost of pressure transducers, the volume of purchase is generally the most influential cost factor because buying in bulk will often lower the price. However, several other base elements must also be considered to ensure the transducer meets your specific needs. These include application-specific requirements that are linked to both functionality and cost:
- Pressure reference and range requirements
- Media compatibility needs
- Accuracy and performance specifications
Then, of course, there are options to consider such as power and output requirements, environmental considerations, and design configurations, all of which will further influence the instrument's price. See Figure 2 for details.
Figure 2. Pressure transducer cost drivers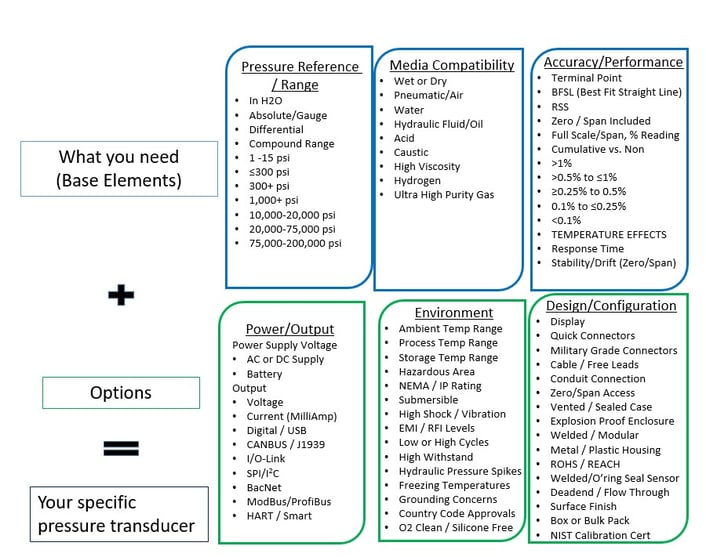
A closer look at the base elements of pressure transducer cost
1. Pressure reference and range requirements
The type of pressure you want to measure (gauge/vacuum, absolute or differential, for example) and the range needed (anywhere from 1 psi to 200,000 psi) determine which transducer technologies can be used in a design. Different technologies such as Chemical Vapor Deposition (CVD) thin film used in the Ashcroft® S1 OEM Pressure Sensor or SiGlas™ Capacitive MEMS used in the Ashcroft® CXLdp and DXLdp differential pressure transducers and have different price points.
2. Media compatibility
The media (gas, liquid, air or other substance) you choose to match your sensor material (wetted parts) will often limit the technology options available. For example, technologies suitable for low-flow differential pressure (DP) air are very different than those for high-pressure hydrogen. So, unless the media is incompatible with most common wetted materials offered for transducers, it is difficult to directly link media to a true impact in cost. Instead, the cost impact of media compatibility is driven by the application media which determines the technology used. See our Material Selection Guide to learn more.
3. Accuracy/Performance
As a general rule in the industrial transducer market, a 0.25% accuracy will cost more than a 1.0% accuracy transducer. If the application and transducer design specifications are very similar, this statement is more relative, but more factors define accuracy.
Here are a few specific accuracy considerations that have the greatest impact on cost:
- Zero and span offset errors can have the largest influence on how accurately your transducer performs as the two combined can put an additional +/- 2% of span error in some products. While this factor is often not included in the typical accuracy statement, a product that is set at zero and span often has a higher performance, value and cost. This value can directly impact a transducer’s installation, setup, field interchangeability and overall cost of ownership.
- Temperature effects, which are often stated as a separate influencing factor on a transducer’s overall performance statement, can add additional error to the statement. This typically equates to a larger error in the output signal as temperature decreases or increases from an ambient temperature point.
Some manufacturers show a total error statement that would include these errors in the overall specification (often referred to as the Total Error Band), what happens to output and accuracy over a particular Operating Temperature Range is important (commonly referred to as Thermal Performance). Taking time to correct the transducer’s output over temperature can be done in a product’s manufacturing and calibration process. The better the accuracy requirement over the operating temperature range, the higher the transducer cost. - Long-term stability (Drift) in pressure sensors is defined by the maximum acceptable change in zero and span values under normal conditions, and typically as a percentage of full scale over 12 months. Stability is inherent to the technology of the instrument and the associated control over the production processes. Put simply, the better the long-term stability of a pressure sensor, the better the product’s Accuracy/Performance and the potential for a higher transducer cost.
Of course, more elements contribute to an overall accuracy or sensor performance, all of which are included in the manufacturer’s accuracy statement.
A closer look at the options affecting pressure transducer cost
1. Power Supply/Output
Output requirements when discussing pressure transducers are becoming less of a cost factor with the incorporation of ASIC/digital technology by most manufacturers for the internal linearization/compensation circuitry. However, certain outputs such as IO-Link or J1939 may require additional circuitry, or even printed circuit boards and may add cost to the product.
Traditional analog compensation circuitry adds cost but can have benefits in the nuclear, military, high-resolution and/or ultra-fast response time applications. Determine what is best in your application and do not expect the cost impact to be very significant if it is common to the industry. Most often, once you define your output requirement, it will lead you to your power supply and input choices.
2. Environment
Three aspects of the external environment to be considered when selecting the proper pressure transducer can also impact cost:
- IP Rating: This comes down to indoor vs. outdoor, and how much water or moisture the transducer will be exposed to over a given The questions are: what IP rating is required for the application and what is the required lifespan? The methods used to vent a transducer (for gauge reference applications) and the transducer housing sealing mechanisms (for applications in IP 67, IP69k, or Submersible), will determine how well the transducer will perform over time in those specified environments.
- Hazardous area: for applications in hazardous locations, you will need to know which type of instrument will provide the best protection: Intrinsically Safe, Non-Incendive (Non-Sparking), or Explosion Proof/Flameproof. In general, Intrinsically Safe and Non-Incendive approved transducers incorporate additional circuitry, component spacing and encapsulation, which increases costs when compared to general-purpose industrial transducers.
Explosion Proof/Flameproof designs have higher costs due to the mechanical requirements to meet approval agency requirements, such as conduit connections with internal wiring isolation, non-flame path venting (for gauge reference) and more robust housing designs. - Electromagnetic radio frequency interference (EMI/RFI) is a result of the general standard of protection being met by most Industrial type transducers bearing the CE mark. However, there are many environments where users wish to incorporate pressure transducers, and the EMI/RFI levels (whether conducted or radiated) exceed those levels.
These environments include, within proximity to some variable frequency drives (VFDs), systems where grounding may not be consistent, railway applications, lightning-related, etc. This requires added cost as a result of additional electronics or construction techniques to shield the internal electronics and maintain output integrity.
3. Design/product configuration
Incorporating a display or a military-type connector will typically add cost to your transducer. One area that may be overlooked is integral cable vs. integral connector. For many manufacturers, an integral cable will cost more to produce vs. an integral connector. However, this would need to be weighed against the cost of the mating cable assembly, or whether an integral cable will be a benefit in the environment (IP67+).
Even though some of the design/product configuration elements are inherent in many designs, as you start to add many of the listed options, you will most often see the price increase at the same time.
For other cost factors in this category, please refer back to the items in Figure 1 above. The initial three base elements will define the available technologies and help establish a base transducer design and starting cost in the market. Following this, and depending on your design, the options chosen can often add to the cost.
Ready to learn more?
As you can see, answering the question about how much a pressure transducer costs is complex. The information above should give you a baseline for understanding what goes into the price so you can be more prepared when you are ready to make your purchasing decision. For more about pressure sensors, here are a few more articles that may interest you:
- Choosing the Right Pressure Sensor: 5 Factors to Consider
- Selecting Electrical Connectors for Pressure Transducers
- What are the benefits of Zero and Span Adjustability?
- What is CVD Technology and Why is it Important in OEM Applications?
- What are the Advantages of Ashcroft Pressure Transducers?
Feel free to contact us to talk to one of our industry experts and get your questions answered.
In the meantime, if you’d like to learn more about mistakes to avoid when selecting pressure sensors, download our guide:
About Mark Zabawa, Director of North America OEM/Direct Sales
Mark Zabawa is the Director of North America OEM/Direct Sales here at Ashcroft. He has spent the past 25+ years in the pressure sensor/transducer industry, with 15 of those years at Ashcroft. Mark has been in roles ranging from Technical Support and Product Management to Regional and National Sales, and his current role is focused on OEM Direct Sales.