What is CVD Technology and Why is it Important in OEM Applications?
Chemical vapor deposition (CVD) is a process used to create highly advanced, field-proven, thin film technology for pressure sensors that are used in mid- to high-pressure applications. These sensors are designed to deliver consistently accurate, reliable and repeatable pressure measurements under some of the most difficult conditions.
If you are an Original Equipment Manufacturer (OEM), you know that your operations are among the most rugged in any industry. As such, you require instrumentation that is both consistently accurate and able to meet the shock, vibration, temperature and high cycle demands of your applications.
As a recognized leader in pressure and temperature instrumentation, Ashcroft pressure transducers offer OEM customers everything they need in a high-quality pressure transducer. Our CVD-based sensors are produced in Japan by our parent company, Nagano Keiki, and are used in many of our pressure sensors, especially those needed for OEMs.
In this article, you will learn how CVD technology works in the manufacturing process, applications where you will find this technology and the benefits it offers to OEM manufacturers and others who use it. When you are done reading, you will see other related resources that will help you learn more about the pressure instruments that incorporate CVD technology and the applications where they are used.
How CVD technology is used to manufacture pressure sensors.
Sensors are built in separate stages:- A layer of silicon sioxide is placed over a stainless-steel diaphragm to act as an insulator.
- A poly-silicon strain gauge is applied over the insulator.
- A lithography process is used to remove specified areas of the strain gauge, leaving only the remaining areas of the diaphragm that will be measured for a change in resistance.
- The poly-silicon strain gauges are connected using gold interconnects to form a Wheatstone Bridge circuit.
This will ultimately be connected to the electronic circuit with wire bonding commonly used in microelectronics. - A proprietary protective layer is then applied as a micro-coating over the strain gauge.
The sensing element is made of stainless steel so it can be welded to pressure fittings to create a secure seal.
Figure 1: Transducer with CVD sensor.
How the pressure sensor works
The electronic circuit is used for calibration and compensation to get an accurate output.
Here’s how the sensor operates:
- Changes in pressure cause the diaphragm to deflect upward.
- This causes a change in the resistance of the 4 strain gauges.
- As the pressure is applied and the diaphragm deflects upward, strain gauges 2 and 3 are in tension mode, and strain gauges 1 and 4 are in compression mode. (see Figure 2)
- With no pressure applied the bridge circuit is “balanced: and the output of the circuit is zero.
- Strain gauges in compression experience a decrease in resistance proportional to the applied pressure.
- Strain gauges in tension experience an increase in resistance proportional to the applied pressure.
Watch the video for an animated view of the process.
Figure 2: CVD sensor strain gauge tension and compression.
CVD pressure transducer outputs
CVD sensor-based transducers can provide multiple outputs, including voltage, ratio metric and current. This makes it a great choice for high-precision monitoring.
Figure 3: CVD pressure transducer outputs.
This technology is also ideal for the following ranges:
Figure 4: CVD pressure ranges.
Why using pressure sensors with CVD technology is important in OEM applications.
Sensors that incorporate CVD sensing technology are known for their superior performance. They are specifically designed for applications that experience high shock, vibration excessive pressure cycling.
There are many reasons why OEMs and others rely on electronic sensors with CVD technology to measure and monitor pressure in their systems. Here are just a few:
- Accuracy. The field-proven polysilicon, and thin film (CVD) pressure sensor technology ensures you meet the requirements of the application.
- Repeatability. It gives you the ability to test pressure with the same tool and get a consistent reading. No need for a span adjustment.
- High cycle life. Technology has the resistance needed to last through millions of cycles.
- Durability. The rugged construction of these pressure sensors is designed with superior protection from shock, vibration, pressure spikes and pulsation that are common in OEM applications.
- Temperature resistance. The welded construction can be used in temperature extremes from -40 to 125 °C.
- All-wetted stainless steel wetted materials. The CVD-based sensors are constructed with stainless steel, with no glues, epoxies or o-rings, and no leakage, offsets or contamination from silicone fill.
Applications where CVD technology excels:
- Mobile Hydraulics. Requires shock and vibration resistance, high cycle life and wide temperature ranges.
- Lift and load systems. Requires repeatability and cycle life.
- Performance racing. Requires superior vibration resistance and high cycle life.
- Pump control. Requires high cycle life.
- Compressor systems. Requires vibration resistance and high cycle life.
- Forestry and mining. Requires extreme vibration resistance.
- Railway. Requires high vibration resistance, high cycle life and excellent repeatability.
- Irrigation Systems: Requires temperature resistance with the ability for freeze-proof protection measures that can be provided as an option with all stainless wetted part designs.
Examples of CVD-based transducers for OEM applications.
Each of the following Ashcroft pressure transducers is manufactured using the CVD method:
- The S1 high-volume sensor is compact and highly configurable. It offers a wide selection of material and connection choices that are designed for vibration, shock and high cycle life.
- The G2 rugged-design sensor is engineered for installations and conditions that also produce substantial vibration, shock and high-cycle life.
- The GV high-vibration sensor offers a durable design providing a perfect choice for harsh operating environments.
- The KD41 offers digital outputs including CANopen, and J1939 for OEM’s requiring these type outputs for the most demanding applications.
- The KM41 highly customizable sensor meets the specific requirements of OEM installations, including mobile hydraulics, pneumatics, industrial equipment and automation.
Do you have the right pressure transducers for your OEM applications?
Now that you know the benefits of CVD and the types of sensors that are designed to provide accurate, reliable and repeatable pressure measurements in the most challenging conditions, are you ready to learn more? Here are a few related articles that you may find interesting:
- OEM High-Pressure Transducer Product Comparison
- How to Protect and Optimize Pressure Transducers on Mobile Hydraulics
- Choosing a Pressure Transducer for Critical Environments
- How Much Do Pressure Transducers Cost? (6 Factors Impacting Price)
- Product Review: S1 OEM Pressure Transducer
Or, reach out today to talk to one of our industry experts and get all your CVD and transducer questions answered.
In the meantime, check out our e-guide, 5 Mistakes OEMs and System Integrators Make When Selecting Pressure Transducers.
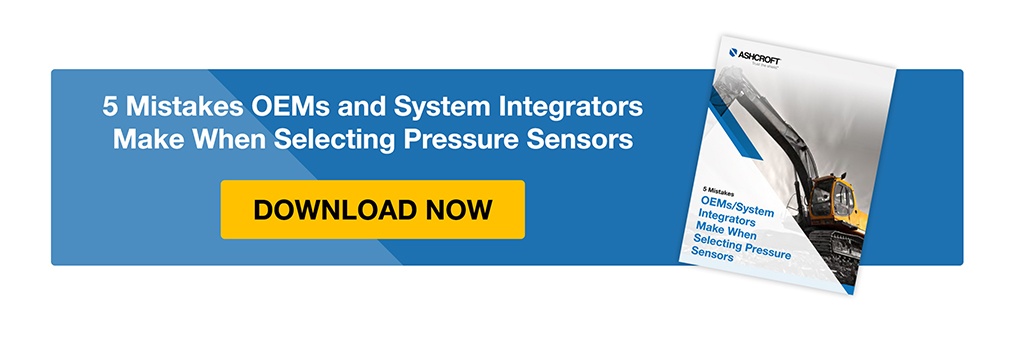