What is a Pressure Gauge?
A pressure gauge is a mechanical instrument that is used to measure and monitor the pressure of air, gases or fluids in process, commercial and industrial systems. These devices operate using the system’s process, meaning they will give you a reading even when you have no power source.
But to understand pressure gauges and how they work, you need to start with the basics. Ashcroft has been making these instruments since 1852 and we wrote this article to give you a foundation of information that you can use as a reference.
Read on to learn about the different types of pressure gauges (process, commercial, industrial, digital) and their functional components. Also become knowledgeable of gauge operating principles and construction, manufacturing standards, sensing and scale elements for various applications, dial options, and more. When you are done reading, you will also find additional resources that may interest you.
Types of pressure gauges and how they are used.
While all pressure gauges are designed to monitor and measure the pressure of air, gas and liquid in a process, how they are used depends on the application. Here’s a quick review.
Process gauges. Process Gauges are designed for use in challenging applications found in process industries like Oil Refineries, Chemical Plants, Wastewater Facilities, Mining and Power Plants. They are used when:
• The safety of operators is a concern when performing process adjustments or repairs in the field
• Very reliable, durable, and easily readable indication of pressure is needed
• Better accuracy and typically a 4” or larger case size is required
Figure 1: Ashcroft® 1279 Process Pressure Gauge.
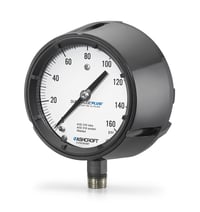
Commercial gauges. Ashcroft defines commercial gauges as an economical pressure gauge primarily used in high volume, original equipment manufacturer (OEM) applications or for general-purpose maintenance applications. These gauges feature:
• Small case/dial size, majority 1 ½” – 3 ½”
• Lower accuracy than process or industrial gauges
• Low cost, sometimes even disposable product
• Customizable with customer logo on the dial
Figure 2: Ashcroft® 1005P Commercial Pressure Gauge.
Industrial gauges. Industrial gauges are all-welded, durable and cost-effective options that are designed to help keep people safe in hazardous environments. You will find them being used in equipment for food and beverage, pharmaceutical, agricultural, scientific and firefighting markets. These gauges feature:
• Slightly larger case/dial size, less than 4-inch inches
• Stainless steel case and socket
• Medium accuracy
• Panel mounting options
Figure 3: Ashcroft® 8009S Industrial Pressure Gauge.
Functional components of a pressure gauge.
While many different components make up a pressure gauge, three primary things make the gauge functional:
A flexible measuring element. This critical component (also known as a tube) is made with an elastic material that moves when a change in pressure occurs.
Movement. The movement from the measuring instrument converts the tube motion into a rotary motion to drive the pointer.
The dial. This gives you a visual indication of the pressure measurement.
Figure 4: Basic Gauge Construction.
High-pressure sensing elements.
The sensing element used will depend on the pressure requirements of the application. Here are some examples.
Bourdon Tube. This is a common component for high-pressure applications and is often made from bronze, steel, stainless steel, Montel® and Inconel®. This type of tube should be welded in the lowest stress area of the tube for the longest, most consistent life span.
Figure 5: Bourdon Tube Construction.
C-Tube. This type of Bourdon Tube (shaped like a “C”) flexes when pressure is applied. They are typically used for pressure ranges between 15 psi and 1000 psi.
Figure 6: Ashcroft® C-Tube.
Helical tubes. These Bourdon tubes are designed for higher pressure ranges, starting at 1000 psi to 30,000 psi. For 50,000 psi to 100,000 psi, Inconel Helical tubes are used.
Figure 7: Ashcroft® Helical Tube.
To learn more about these sensing elements, read Types of Bourdon Tube Construction.
Low-pressure sensing elements.
Different types of sensing elements are used on gauges designed for low-pressure applications. Here are several examples for your reference.
Diaphragm capsule. The elastic element of the diaphragm capsule is made from two convoluted diaphragm plates that form a capsule. It is a very simple, straightforward design that expands or contracts in response to changes in pressure.
Figure 8: Diaphragm Capsule.
Bellows. These sensing elements provide the same function as a diaphragm capsule but with a different technology. The thin-walled, convoluted elastic construction expands or contracts up and down (not left to right) as pressure changes.
Figure 9: Bellows Technology.
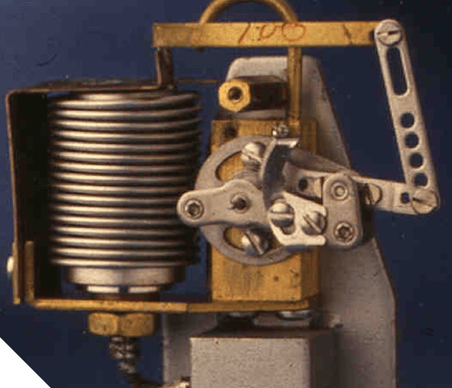
Spiral tube/Direct drive coil. With this element, the coil turns and unwinds when pressure is applied to the coil tube which causes the dial to move. This motion will directly drive the pointer without the use of a movement.
Figure 10: Direct Drive Coil.
Magnetic sensing elements for differential pressure gauges. When pressure is applied to either side of the piston, the piston will move back and forth based on which side has the higher pressure. The piston has a magnet in it which rotates the magnet in the pointer.
Figure 11: Magnetic Sensing Element.
Dual Diaphragm Sensing Elements for Differential Pressure Gauges.
Here’s how it works:
- The two diaphragms (5) are mechanically linked by a rigid connecting rod (6).
- The cavity between the two diaphragms is filled with hydraulic fluid.
- When there is a difference in pressures acting on the two diaphragms, they are deflected causing a displacement of the connecting rod (6).
- The precision mechanism (3,2 & 1) translates this displacement to an angular movement of the dial pointer.
Figure 12: Diaphragm Sensing Elements.
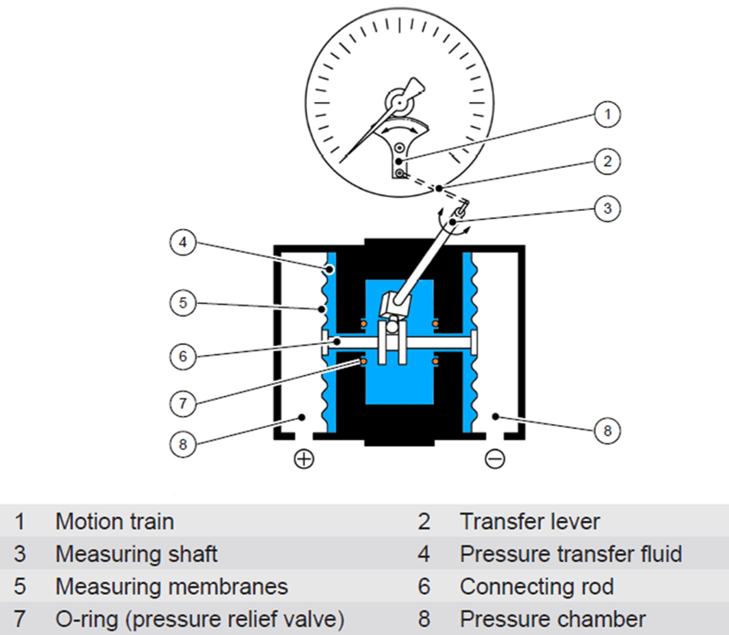
Gauge Case Types
There are two basic types of gauge cases: open front or solid front.
Open Front – No partition or barrier is placed between the pressure element and the window. These cases are less expensive and most often used in low-pressure commercial applications.
Solid Front – A partition with minimal openings is positioned between the pressure element and the window. These cases are more expensive but have an added safety feature. This is important for use in high-pressure applications in process plants, for example, that have the possibility of rupturing.
Pressure Relief Plug Feature – A plug in the gauge case wall that will vent the case in the event of an element leak.
Case materials – Gauge cases are typically made with Thermoset/Thermoplastic, Aluminum and Stainless Steel or Black Metal.
Figure 13: Solid Front Gauge and Rear Blow Out Plug.
To learn more about case options, read Solid Front vs. Open Front Pressure Gauges.
Gauge windows and dials
There are many different styles of window and dial options, all of which depend on the application requirements and the model gauge you select. Certain gauges, for example, are liquid-filled or have temperature restrictions, which will affect the type of window option available. Here are the most common window types offered for pressure gauges:
• Glass
• Safety Glass
• Acrylic
• Polycarbonate
• Polysulfone
Before you select the window type, read your data sheet to see what window choices you have.
Gauge dial sizes range from 1.25 to 16 inches. Other than the application, there are two primary factors to consider when selecting the dial size of your gauge: location and accuracy requirements.
1. Location. This refers to the distance that you want to be able to read the dial. For example, if your gauge needs to be visible from a far distance would require a larger dial size. The size you select will depend on where the gauge is positioned in relation to the operators who need to view it.
2. Accuracy. Because the dial size is part of the accuracy, there are recommended dial sizes, depending on your accuracy requirements. Generally, the larger the size, the more accurate the gauge.
Any manufacturer that makes pressure gauges must follow certain global ASME standards: ASME B40.100 standards or EN 837-1 Standards, which are specific to European regions. These standards ensure all gauges function the same way to provide a visual window into the operating process.
Figure 14: ASME B.40.100 Standards.
Figure 15: EN 837-1 Accuracy Standards.
Customizable dial options.
Manufacturers can tailor the dials to show what zone your pressure reading is in (low, normal, high), call out a false reading, or highlight other information you request. They can also customize dials with a company logo and offer scale options.
Figure 16: Customizable Dial Options.
Figure 17: Customizable Dial Options.
Figure 18: Dual Scale Elements.
Gauge mounting.
When it comes to mounding your pressure gauge, you also have many options, including:
• Stem mount, lower connect
• Wall/surface mount, lower connect
• Panel mount, back connect
• U-clamp flush mount, back connect (for panel mounting)
• Front flange flush mount, back connect (for panel mounting)
For more information, read our article, “Choosing the right pressure gauge dial size”.
Ready to learn more?
Now that you know the basics about pressure gauges and how they work, you likely have more questions. Here are a few helpful resources to help you take the next step in building your knowledge on the subject:
- Seven Steps to Select a Pressure Gauge
- Choosing the Right Pressure Gauge Dial Size (ashcroft.com)
- How Can I Order Custom Dials for Pressure Gauges?
Or, to speak with someone directly, feel free to contact one of our product experts with any questions you have. In the meantime, check out our pressure gauge selection tool to help you find the best instrument for your needs.
About Dave Dlugos, Product Technical Leader
Dave Dlugos has a BSEE degree and 40 years of experience in the measurement industry performing design engineering and product management. He has earned 4 U.S. patents and joined Ashcroft in 2007, currently as the Product Technical Leader. He is a senior member of the International Society of Automation (ISA), past ISA District 1, Vice President, past ISA water and wastewater division board member and the past President of CT Valley ISA Section.