What is an Isolation Ring?
Isolation rings are also known as isolators. They are designed to protect pressure-measurement instruments from the damaging effects of corrosive media in water/wastewater treatment plants, chemical processes, and mining facilities. To fully appreciate the importance of using these instruments in your operation, we need to start with a basic understanding of how they work.
Ashcroft has been in the pressure and temperature instrumentation business since 1852, and we wrote this article for the industry novice. We hope you can use it as a foundation for understanding the important role isolation rings play in challenging applications.
Read on to learn how isolation rings protect pressure-sensing instruments in your applications, the three most common types of rings, how they are constructed and the primary benefits of using these instruments. When you are done reading, you will also find additional, related resources in case you want to go beyond the basics of this topic.
Why are isolation rings needed in water/wastewater applications?
Domestic and industrial wastewater contains physical, chemical, and biological waste that can be challenging to monitor and control during treatment. The goal of treatment is to remove contaminants from wastewater, with characteristics varying based on the source and treatment phase.
For instance, domestic wastewater faces challenges with slurries, especially in the primary phase. Isolation rings and flush diaphragm seals with compatible media materials are essential for protecting pressure instruments in wastewater treatment from corrosion and clogging. Isolation rings are used with pressure instruments for tasks like monitoring tank levels, screens, filters, pipe pressure, and flow.
Three stages of water/wastewater treatment that rely on isolation rings.
1. Primary wastewater treatment process
In this stage, sewage moves through big tanks known as pre-settling basins, primary sedimentation tanks, or primary clarifiers. Solid waste sinks to the bottom of the tank, while grease and oils float to the top and are removed. These tanks typically use mechanical scrapers that push the waste toward a hopper for the next treatment stage
2. Secondary treatment
The secondary treatment breaks down the organic matter in sewage, which includes human waste, food waste, soaps, and detergents. Most municipal plants use aerobic biological processes to treat the settled sewage.
3. Tertiary treatment
This final treatment stage may include multiple processes, including decontamination to improve waste quality before it is released into the environment.
How do isolation rings work?
Isolation rings attach to the process connection of pressure instruments to create a secure barrier separating the instruments from the process media. The flexible 360-degree inner cylinder prevents clogging in the process and ensures accurate and reliable pressure transfer to the pressure devices.
They are made with a flexible bladder that is assembled to a body and clamped together with two flanges (see Figure 1). The flexible bladder, aka membrane or liner, is filled with the fill fluid. Process pressure presses on the bladder. This in turn pushes the fill fluid into the pressure instrument that is attached to the ring. One or more instruments can be mounted to an isolation ring.
Figure 1: Isolation Ring Construction.
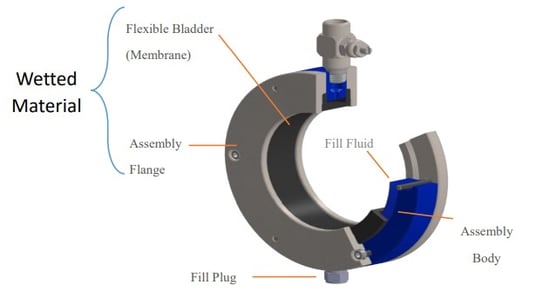
Three types of isolation rings
Three types of isolation rings are most commonly used in water/wastewater applications:
1. Wafer Isolation Ring
Wafer rings like the Ashcroft® 80 Isolation Ring provide complete instrument protection and are ideal for applications that require continuous pressure measurement. The ring is mounted in line with the process piping and is designed to eliminate process accumulation so the pressure instrument can provide accurate measurement readings. This style of ring can fit between piping flanges and is available in 2" to 20" pipe sizes.
Figure 2: Wafer isolation ring installed in the process.
2. Bolt Thru Isolation Ring
Similar to wafer rings, bolt-thru rings like the Ashcroft® 81 Isolation Ring are also perfect for applications that need continuous pressure measurement. The mounting bolts pass through the ring and the pipe flanges. These isolation rings are also designed to eliminate process accumulation so the pressure instrument can provide accurate measurement readings. This style of ring can fit between piping flanges and is available in 1" to 10" nominal pipe sizes.
Figure 3: Wafer isolation ring installed in the process.3. Threaded Isolation Ring
Threaded rings like The Ashcroft® 82 Isolation Ring serve the same purpose as the wafer and bolt-thru options, but these are installed in line with the process piping using 1/2 - 2 NPT process connection options. They are economically designed, offer short lead times and provide a variety of fill fluid options for every application.
Figure 4: Threaded isolation ring installed in the process.
To learn more about these different options, watch our video.
How to select the right isolation ring for your application.
Before you select which isolation ring you will use in your application to protect your pressure instrument, consider the following:
1. Select the proper wetted materials and fill fluid for the process to be measured. The temperature range of the process needs to be factored into the fill fluid and liner material decision.
2. Determine the displacement required. The displacement of the isolation ring needs to be larger than the displacement of the instruments to function correctly. This is very important when placing multiple instruments on an isolation ring. It may be necessary to consult with the manufacturer to determine if the instruments and chosen isolation ring combination will work correctly.
3. Evaluate the required measurement accuracy and resolution needed. There are additional errors added when attaching instruments to the isolation rings. Be sure to check span and zero of the instruments after they have been mounted to the isolation rings to correct or account for any errors. For example, pressure switches should always be set after installation to the isolation ring.
Temperature variations can introduce errors from the expansion or contraction of the filling fluid. These errors can be predicted by knowing:
- the specifics of the fill (i.e. total internal volume and coefficients of expansion)
- the seal/instrument assembly (i.e. volumetric spring rate and pressure range)
- the temperature influences (i.e. ambient and process temperatures)
The error induced is directly related to the change in the internal volume of the fill in the assembly. This error is not a function of the instrument pressure range. However, the final percent error does depend on the range. A low-pressure range instrument will have a higher error than a high-pressure range instrument.
To minimize the temperature effect error for low-pressure ranges, it is best to select instruments with less internal volume. In other words, the smaller the internal volume of an instrument the less fill fluid to expand or contract.
Ready to go beyond the basics?
Now that you know the basics about pressure gauges and how they work, you likely have more questions. Here are a few helpful resources to help you take the next step in building your knowledge on the subject:
Or, to speak with someone directly, feel free to contact one of our product experts with any questions you have. In the meantime, download our water/wastewater industry solutions guide.
About Dave Dlugos, Product Technical Leader
Dave Dlugos has a BSEE degree and 40 years of experience in the measurement industry performing design engineering and product management. He has earned 4 U.S. patents and joined Ashcroft in 2007, currently as the Product Technical Leader. He is a senior member of the International Society of Automation (ISA), past ISA District 1, Vice President, past ISA water and wastewater division board member and the past President of CT Valley ISA Section.