What is a Pressure Switch?
A pressure switch is a control device that senses changes in pressure and mechanically opens and closes an electrical circuit at a pre-determined point. Unlike other pressure instruments like pressure gauges and pressure sensors that measure and monitor pressure, switches are a bit more complicated.
Ashcroft is an industry leader in pressure measurement instrumentation and created this article to provide a basic foundation of information about switches for the industry novice.
Read on to learn about the different types of pressure switches, common applications, how they operate, key terms, switch accuracy, activation methods and more. When you’re done reading, you will also find additional resources about switches that may interest you.
Where are pressure switches used?
You will find pressure switches in numerous applications in hydraulic, oil and gas industries as well as agriculture, chemical/petrochemical and water/wastewater operations among others. They are typically used with pumps, boilers, burners, power supplies and other applications.:
Figure 1: Pressure Switch Industry Applications.
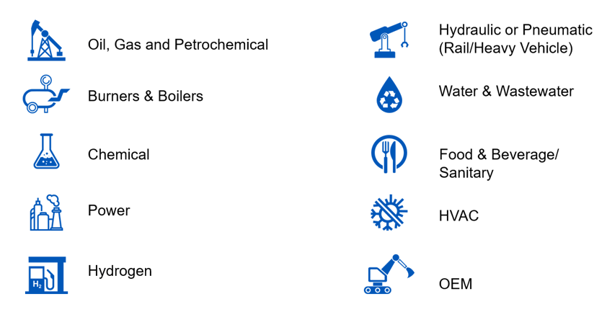
How does a pressure switch work?
In a pressure switch, when pressure from the process is applied, here’s what happens:
1. Pressure is applied by a pressure source through the process connection.
2. This pressure applies a force on the actuator (also known as the diaphragm), causing it to move upward.
3. However, an opposing force created by the spring and adjusting nut keeps the actuator from moving up.
4. To move the actuator assembly, the force from the pressure source must be greater than the opposing force from the spring.
5. The switch setpoint is controlled by the Adjusting Nut:
- When the adjusting nut is raised, it will decrease the force in the spring (lowering the set point)
- When the adjusting nut is lowered, it will increase the force in the spring (raising the set point).
6. When the force of the process pressure finally overcomes the force of the spring, the actuator will push upwards, moving the push rod and causing the switch to change state.
Figure 2: Pressure Switch Operational Elements.
What are the key elements of pressure switches?
Switching element (also known as a microswitch). A micro switch changes state when the pushrod presses and releases the button on the micro switch. This causes the internal arm to move from one of the internal contacts and connect with the other contact. Learn more with our blog, Choosing the Right Microswitch for Your Application.
Figure 3: Switching Element – Normally Open and Normally Closed.
Normally Open (NO) Contact. The NO contact is open when the pressure is below the set point and is closed when the pressure exceeds the set point. For example, a switch with a set point of 10 psi will be open when the pressure is below 10 psi (shown top left) and close when the pressure is above 10 psi (see above).
Normally Closed (NC) Contact. An NC contact acts oppositely. The switch is closed when the pressure is below the set point and opens when the pressure exceeds that set point. For example, a switch with a setpoint of 10 psi will be closed when the switch is below 10 psi and open when the switch is above 10 psi (see above).
The above NO and NC contacts work for pressure switches. However, if you are using a vacuum switch (one that has a pressure less than atmospheric or barometric, the operation is reversed.
Microswitch configurations. There are two types of microswitch element configurations:
- Single Pole Double Throw (SPDT)
A SPDT switch element has one normally open, one normally closed, and one common terminal. This switch allows for 1 set point and can be wired to either a Normally Open or Normally Closed circuit.
Figure 4: Single Pole Double Throw (SPDT).
-
Double Pole Double Throw (DPDT)
The DPDT switch element, has 2 separate contacts, each with 1 normally open, 1 normally closed and one common terminal. These types of switches allow for wiring into two separate loads which will activate at the same set points. The user can wire each circuit to either the Normally Open or Normally Closed contacts.
Figure 5: Double Pole Double Throw (DPDT).
To get a DPDT switch element, manufacturers take two SPDT switches and mount them into a special bracket that allows them to actuate at the same setpoint.
Pressure sensing element. The pressure sensing element moves or displaces proportionally to the pressure (or vacuum) that is being applied. This can be either a diaphragm or a piston.
- Diaphragm. Choosing the proper diaphragm is important because the diaphragm is part of the pressure switch that is exposed to the air, gas, or liquid being measured. Simply put, the diaphragm material you select must be compatible with the process media of the application.
Here are examples of the diaphragm materials suited for many different types of applications:- Buna-N or Viton™ (hydraulic, oil or gas applications)
- Teflon™ (chemical applications)
- Stainless steel (steam, water or wastewater applications)
- Monel® (NACE-related applications)
Each material has a specific temperature and pressure range that it can handle without being damaged.
Figure 6: Diaphragm Materials Temperature and Pressure Ranges.
- Piston. Piston elements are used for higher-pressure designs, typically 1000 psi or greater. Pistons are usually made of stainless steel and have an O-ring seal. It is important to make sure the stainless steel material and the O-ring material are compatible with the process.
Proof & Burst Pressure. It is important to understand both pressure types to be sure you are using switches that will meet your application.
- Proof pressure is the maximum pressure that can be applied to a pressure switch without causing damage. Proof pressure is determined under strict laboratory conditions, including a controlled rate of change in pressure and temperature. This value is for reference only.
You will need to consult the factory for applications where the switch must operate at pressures above nominal range or reference temperature. Knowing the proof pressure of a switch may allow for it to be used in applications where you originally thought it was not possible.
- Burst pressure is the maximum pressure that can be applied to a pressure switch without causing leakage or rupture. Typically burst pressure is at least 400% of the range of the switch. Switches that are exposed to pressures greater than the burst pressure can be permanently damaged.
The Ashcroft© A-Series Watertight Pressure Switch, for example, has the following proof pressure ratings and maximum working pressure ratings:
Figure 7: Ashcroft A-Series Pressure Ratings.
Differential and static pressure. Differential pressure is a measurement of the difference in pressure between two points in a system. Static pressure is the normal operating pressure of the system.
In many filter or strainer applications, it is important to know when the filter needs to be cleaned or replaced. As fluid moves through a filter debris causes a pressure drop from one side of the filter to the other.
- 20 psi = static pressure normal pressure flowing through the system (both sides of the filter)
- 5 psi = setpoint the operator wants to know when there is a 5 psi pressure drop in pressure between the two sides of the filter. (This is also known as the differential pressure.)
A switch is used to monitor the flow going in and out of the filter and when the pressure on the outside drops to 15 psi (which is a 5 psi differential, thus a setpoint of 5 psi), the operator gets a switch closure telling him to clean or replace the filter.
Figure 8: Monitoring Flow with Pressure Switches.
Repeatability (Accuracy). Repeatability is the ability of the switch to repeatedly open and close at the same set point. For most Ashcroft switches, including our B-Series products, our accuracy is +/– 1% of span. So, for a unit with a 100 psi range the accuracy is +/– 1 psi. If you have a set point of 50 psi, the switch should close every time somewhere between 49 to 51 psi.
Deadband (also known as hysteresis or differential). Since pressure switches are mechanical devices, the physics of the device does not allow the switch to reset as soon as the pressure drops below the set point.
As you can see in the chart below, as pressure rises the switch trips at the set point, when the pressure drops the switch does not reset immediately, this is the dead band of the switch. Read, What is Deadband on a Pressure Switch and How Does it Work to learn more.
Figure 9: Deadband Setpoint and Reset Point.
It is important to note that:
o On an increasing set point, the switch will reset at a lower pressure point.
o On a decreasing set point, the switch will reset at a higher pressure point.
The pressure range, diaphragm material, and switching element are all variables that dictate the deadband of a switch. How big or small it is depends on these variables.
Approvals. Pressure switches are electrical devices with many explosion-proof and watertight applications that require agency approvals, such as electrical safety, hazardous locations and safety integrity levels (SIL).
Go beyond the basics.
Now that you have a basic understanding of pressure switches and how they work in different applications, you may be ready to dig in a little deeper. Here are a few related articles that can get you started.
- Choosing a Pressure Switch: 9 Factors to Consider
- Pressure Switch Fundamentals (webinar)
- Class and Division Codes on Explosion-Proof Pressure Switches
- What is SIL Certification for Pressure Switches?
Or, to speak with someone directly, feel free to contact one of our product experts with any questions you have. In the meantime, download our e-book to learn more.
About Dave Dlugos, Product Technical Leader
Dave Dlugos has a BSEE degree and 40 years of experience in the measurement industry performing design engineering and product management. He has earned 4 U.S. patents and joined Ashcroft in 2007, currently as the Product Technical Leader. He is a senior member of the International Society of Automation (ISA), past ISA District 1, Vice President, past ISA water and wastewater division board member and the past President of CT Valley ISA Section.